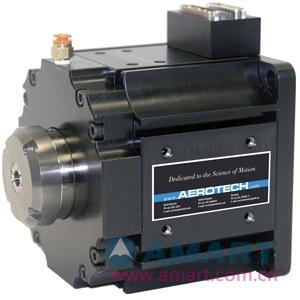
Aerotech的ACS系列转台具有集成的ER弹簧夹头或3爪夹持器配置为范围广泛的材料和应用提供自动材料处理能力。
● 通孔便于产品馈通
● 常闭或常开夹钳选项
● 低惯量轴提供最大加速度
● 直驱无刷电机和编码器
● 集成旋转接头
The collet chuck on the ACS-150 accepts either ER25 or ER40 series collets. These collets are readily available from machine-tool component suppliers in sizes that support tube diameters from 0.5 mm to 30 mm. ER collets provide excellent run-out characteristics for applications requiring high-precision gripping of tubular material. The collet is retained with a threaded retaining cap enabling quick changeover. It is configured in a “fail-safe” normally closed mode where full clamping force is applied when no air pressure is present.
Both the ACS-150 and ACS-200 support three-jaw grippers with clear apertures for product feed-through. All gripper assemblies are configurable as either normally-open or normally-closed with various jaw strokes to support a wide range of material sizes. The gripper can be fitted with custom jaws for the handling of materials with non-round profiles such as square or hexagonal bar stock. The normally-open and -closed options also provide the ability to grip either the O.D. or I.D. of the material.
集成旋转接头
Air is delivered to the collet or gripper assembly through an integral rotary union. The 3-jaw grippers use a seal-based rotary union design while the ER collet option uses a seal-less, frictionless design. This 100% noncontact rotary union design ensures a lifetime of maintenance-free operation. The combination collet chuck or gripper and rotary union assembly also have significantly less friction and inertia than external assemblies created from discrete parts. This reduced inertia improves system performance by allowing higher peak acceleration and reducing position error during laser machining operations.
To maximize positioning performance the ACS series utilizes direct-drive brushless motor technology. Direct-drive technology is optimized for 24/7 production environments, as there are no brushes to replace and no gear trains or belts to maintain. Direct-drive also provides quicker acceleration and higher top speeds than gear- or belt-driven mechanisms, which yields higher total overall throughput.