ATS1500 机械轴承丝杠平台 | ATS1500 Mechanical-Bearing Ball-Screw Linear Stage | 交叉滚柱轴承滚珠丝杠驱动直线定位平台
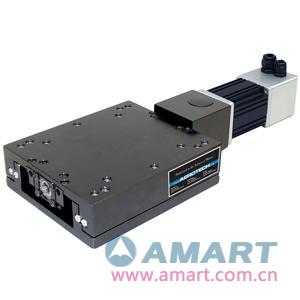
The ATS1500 series provides a flexible platform that makes it an outstanding selection for use as a general purpose positioner.
ATS1500 Specifications
Model | ATS15010 | ATS15020 | ATS15030 | |
---|---|---|---|---|
Travel | 100 mm | 200 mm | 300 mm | |
Drive System | Super Precision Ground Ball Screw (P), Precision Ball Screw (B), Lead Screw (L); Brushless Servomotor (BMS60-A-D25-E1000H) | |||
Bus Voltage | Up to 160 VDC | |||
Continuous Current | Apk | Up to 2.3 A | ||
Arms | Up to 1.6 A | |||
Feedback | Noncontact Rotary Encoder (1000 line) | |||
Resolution | 4 mm/rev Lead | 1.0 μm (40 μin) @ 4000 steps/rev Motor Resolution | ||
0.2 in/rev Lead | 1.25 μm (50 μin) @ 4000 steps/rev Motor Resolution | |||
Maximum Travel Speed(1) | 4 mm/rev Lead | 140 mm/s | ||
0.2 in/rev Lead | 180 mm/s | |||
Maximum Load(2) | Horizontal | 70.0 kg | 115.0 kg | 135.0 kg |
Vertical | 25.0 kg | 35.0 kg | 45.0 kg | |
Side | 45.0 kg | |||
Accuracy |
Super Precision Ball Screw |
±4 μm | ±8 μm | ±12 μm |
Precision Ball Screw | ±8 μm | ±16 μm | ±24 μm | |
Lead Screw | ±16 μm | ±32 μm | ±48 μm | |
Bidirectional Repeatability |
Super Precision Ball Screw |
±1.0 μm | ||
Precision Ball Screw | ±2.0 μm | |||
Lead Screw | ±4.0 μm | |||
Straightness and Flatness | ±4 μm | ±8 μm | ±12 μm | |
Nominal Stage Weight | Less Motor | 3.1 kg (6.8 lb) | 5.0 kg (11.0 lb) | 7.0 kg (15.4 lb) |
With Motor | 4.2 kg (9.3 lb) | 6.1 kg (13.4 lb) | 8.1 kg (17.9 lb) | |
Construction | Aluminum Body; Black Anodize Finish |
- "L" grade screws are limited to less than 75 mm/s. Excessive duty cycle may impact stage accuracy.
- Payload specifications are for single-axis system and based on ball screw and bearing life of 250 km (10 million inches) of travel.
- Specifications are for single-axis systems measured 25 mm above the tabletop. Performance of multi-axis systems is payload and workpoint dependent. Consult factory for multi-axis or non-standard applications.
-
Cantilevered load capability of the ATS1500
Dimensions
-
ATS1500
Ordering Information
Ordering Example
ATS15 | -010 | - | -2 | -02P | -BMS | -NC | - |
Ordering Options
Series | Travel (mm) | Stage Construction Options | Bearing System | Drive Screw | Motor | Limits | Options |
---|---|---|---|---|---|---|---|
ATS15 |
-010 -020 -030 |
/VAC3 /VAC6 |
-2 |
-02L -02B -40L -40P |
-BMS -SM -NM |
-NC -NO -9DU -FLY |
-BRK |
ATS1500 Series Linear Ball-Screw Stage
Option | Description |
---|---|
ATS15010 | 100 mm (4 in) travel stage with limits |
ATS15020 | 200 mm (8 in) travel stage with limits |
ATS15030 | 300 mm (12 in) travel stage with limits |
Stage Construction Options
Option | Description |
---|---|
/VAC3 | Vacuum preparation of stage to 10-3 torr |
/VAC6 | Vacuum preparation of stage to 10-6 torr |
Bearing System
Option | Description |
---|---|
-2 | Crossed roller bearing system |
Drive Screw
Option | Description |
---|---|
-02L | 0.2 inch per rev lead screw (not recommended for vertical applications) |
-02B | 0.2 inch per rev precision ball screw |
-40L | 4 mm per rev lead screw (not recommended for vertical applications) |
-40P | 4 mm per rev super-precision ball screw |
Motor
Option | Description |
---|---|
-BMS | Brushless servomotor with connectors and 1000-line encoder; requires cable (BMS60-A-D25-E1000H/) |
-SM | Stepping motor with connector and home marker pulse (one per rev); requires cable (101SMB2-HM/) |
-NM | No motor or encoder |
Limits
Option | Description |
---|---|
-NC | Normally-closed end of travel limit switches (standard) |
-NO | Normally-open end of travel limit switches |
-9DU | With 9-pin limit connector |
-FLY | With flying leads |
Options
Option | Description |
---|---|
-BRK | 24 VDC spring-set motor brake for NEMA 23 motor |
Accessories (to be ordered as separate line item)
Option | Description |
---|---|
ALIGNMENT-NPA | Non-precision XY assembly |
ALIGNMENT-NPAZ | Non-precision XZ or YZ assembly |
ALIGNMENT-PA10 | XY assembly; 10 arc sec orthogonal |
ALIGNMENT-PA10Z | XZ or YZ assembly with L-bracket; 10 arc second orthogonal |
HDZ2/AP1500 | English right angle bracket/mounting plate for Z-axis configurations |
HDZ2M/AP1500 | Metric right angle bracket/mounting plate for Z-axis configurations |
Note: Cannot use longer than 200 mm travel as Y or Z axis without custom adapter plates. Please consult factory.
*Please go HERE for complete information on XY, XZ and YZ assembly options.
*Please go HERE for complete information on motor orientation options.