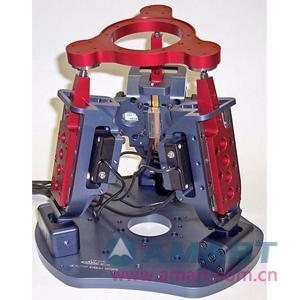
Hexapods are inherently by nature of the design and the chosen components of the ALIO Hexapod faster settling times after a move with no servo dither or flexure bend on point.. In addition, the frictional force between the linear motor and the motion linkage means no hysteresis or loss of position if the power is lost. The Hexapod and Tripod with additional preparation can meet Class 10 clean room standards. We can also provide systems that will work in vacuum chambers 10e-10 TORR.
The performance of ALIO Hexapods is an order of magnitude more precise than Hexapods of the past. With complex forward and inverse kinematic equations in a parallel structure the controller system is critical.
ALIO Hexapod has 2 controller choices that are integrated into the total system. The Delta Tau and the ACS motion systems are both high end motion controllers with 4096 interpolation allow for 5nm encoder resolution on each link of the Hexapod. The motion controller provides the necessary structure to enable the user to easily implement and execute complex kinematic calculations. Kinematic calculations are required when there is a non-linear mathematical relationship between the tool-tip coordinates and the matching positions of the actuators (joints) of the mechanism, typical in non-Cartesian geometries.
This capability permits the motion for the machine to be programmed in the natural coordinates of the tool-tip, usually Cartesian coordinates, whatever the underlying geometry of the machine. The "forward-kinematic" calculations use the joint positions as input, and convert them to tool-tip coordinates.